Pretend for a minute that you've developed a new mathematical model that explains cell growth in plants.
Rather than expanding smoothly like a balloon, you hypothesize, cell walls behave as if they were a pixilated surface, expanding on a pixel-by-pixel basis to the internal pressure that drives cell growth.
Your theory is confirmed by the fact that it predicts measured cell pressure much more accurately than the currently accepted model.
To test your hypothesis in the lab — and create publishable data that could lead to a more useful and universal understanding of plant growth — here's all you need: a multi-sided, 16-and-a-half-inch-tall chamber of thick glass panels, stainless steel and acrylic, with a pressurized cylinder on top for exchanging gasses, into which a giant celled alga can be suspended in water and subjected to eight atmospheres of pressure.
‘Not exactly an off-the-shelf item.
Philip Lintilhac and Chunfang Wei, who developed the cell growth theory, weren't fazed, however. They’re plant biology research scientists in UVM’s College of Agriculture and Life Sciences (CALS).
They did what countless other UVM faculty have done before them: they trooped down to East Avenue, where UVM's Instrumentation and Model Facility (IMF) is located, and placed an order for the contraption they'd dreamed up — or at least a vague early conception of it.
Since the mid 1960s, IMF has built thousands of custom prototype devices for UVM faculty to use in their research. Today about 200 projects a year wend their way through the shop, a cluttered skunk works of computers displaying CAD designs, which rim a lumbering herd of large, steel-gray, computer-controlled milling machines.
Napkins and CAD
The devices that IMF specializes in are, by nature, unique: the product of a researcher's imagination and best guess about how to answer a scientificquestion.
The process of going from concept to finished prototype is as varied as the devices the shop creates, says Tobey Clark, who's directed IMF and its sister unit, Technical Services Partnership (together the units are known as Instrumentation and Technical Services) since the mid-1990s.
Some researchers come in with a verbal description, he says. "Then they sketch something out on a piece of paper or a napkin." Others come in with a more or less complete CAD drawing.
"Throughout the process," he says, "we're always offering our expertise on what can be manufactured, what can be developed electronically, the best methods to do that, the most economical, the highest accuracy, whatever the focus is."
Scented Pacifiers
At first blush, some of the items in IMF's product line can seem odd.
Take one called an olfactometer, built by two of the three instrument developers at the IMF's East Avenue headquarters, Doug Gomez and Mike Fortney (the other is Carl Silver; a fourth, Guy Kennedy, is based at HSRF).
The brainchild of associate neurology professor Peter Bingham, the device is designed to measure -- with rigorous experimental controls -- whether prematurely born infants suck more frequently on a special pacifier, one that aims whiffs of breast milk scent at the baby's nose, than on an ordinary one.
If the device — a complex piece of electronics and machined components — shows that the milk-scented pacifier does indeed do the job, as Bingham's earlier research suggests, the ramifications could be significant. Neonatal intensive care units might routinely use the pacifiers, which were developed by Bingham, to help premature infants nourished via feeding tubes become more practiced at sucking, allowing them to leave the ICU more quickly and begin bonding with their mothers at home.
Printing in 3-D
Last year IMF welcomed into its fold a spiffy new piece of equipment that Clark is especially high on: a "3-D printer" that can create prototypes and models in a few hours, which previously took days using conventional methods. The machine builds them film-like, layer by layer — using a variety of hard or soft laminates — as specified by a CAD drawing controlling it.
Increasingly, IMF is working with students, and with a growing collection of Vermont entrepreneurs, many of whom are fans of the 3D printer.
One, Omni Medical Systems in Milton, is using it to develop prototypes for a new generation of "flight extenders" for jet pilots, plastic fittings worn inside a flight suit for those times when a rest stop is not near.
Although IMF's work is vital for an institution aspiring to be one the nation's premier small research universities, more down-to-earth impulses seem to be animating staff day-to-day: something like the joy of working with a team to get a design just right.
That's evident in the vigorous back and forth between Lintilhac, Wei and Gomez, who's taking the lead on the pressure chamber project, as they huddle around a computer screen at IMF. Using a program called SolidWorks, Gomez twists and turns a schematic of the design he created, based on a Lintilhac sketch, adding new features at his clients' request on the fly.
"They're wonderful people to work with," says Lintilhac, who's used half a dozen prototypes developed by IMF in his work, including an earlier generation of the pressure chamber that showed the new cell growth theory was promising.
"I don't know what I would do without them."
Here’s more information on CALS plant biology research.
CAPTION: Doug Gomez of IMF, from left, stands by as Chunfang Wei and Phiipl Lintilhac of CALS plant biology take a first look at a special pressurized chamber he built and helped design for them. The device may help the researchers come to a new understanding of the biophysics of plant cell growth. ~Sally McCay photo.
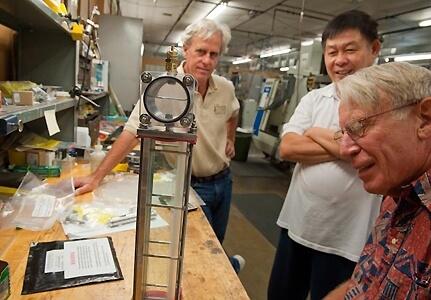
Plant Biologists Rely on Custom Lab
ShareSeptember 15, 2010