At the College of Engineering and Mathematical Sciences, we are more than educators. We are a community of problem solvers, inspiring each other to build true world solutions that will lead to healthy, sustainable societies.
Our approach is personal, fostering a culture of collaboration that’s as driven by student-to-student connections as by our world-class faculty and advanced research opportunities. You may enter UVM a little unsure, eager, and excited for the next chapter. By the time you’re ready to leave, you’ll be poised to change the world.
academics A hands-on, team-based approach
By the numbers
- 15 accelerated master's programs in STEM-related fields
- 8 petaflops supercomputer
- Top 10 "Most Innovative Tech Hub" - Forbes
In the news
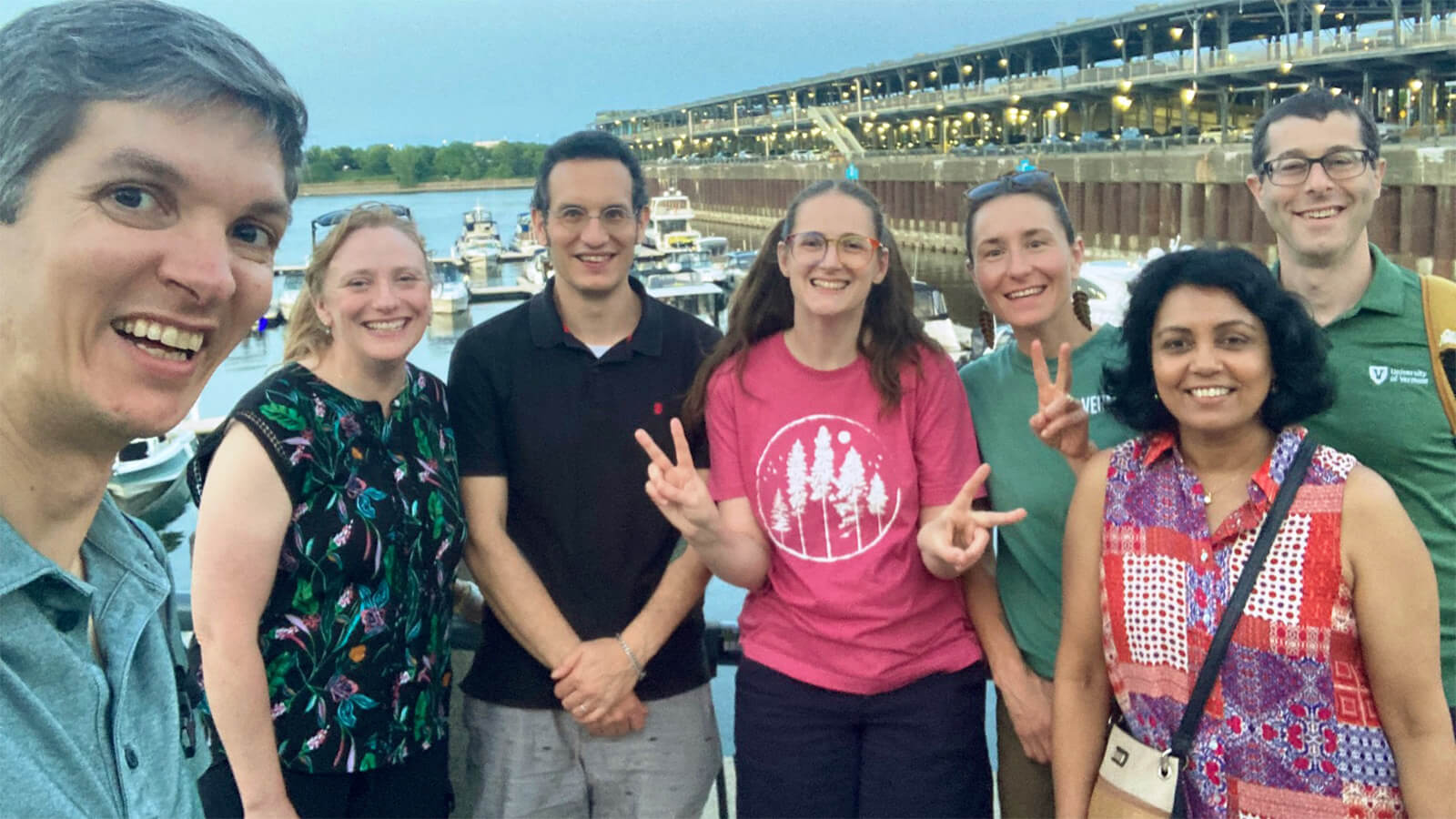
Building Excellence in Engineering Education
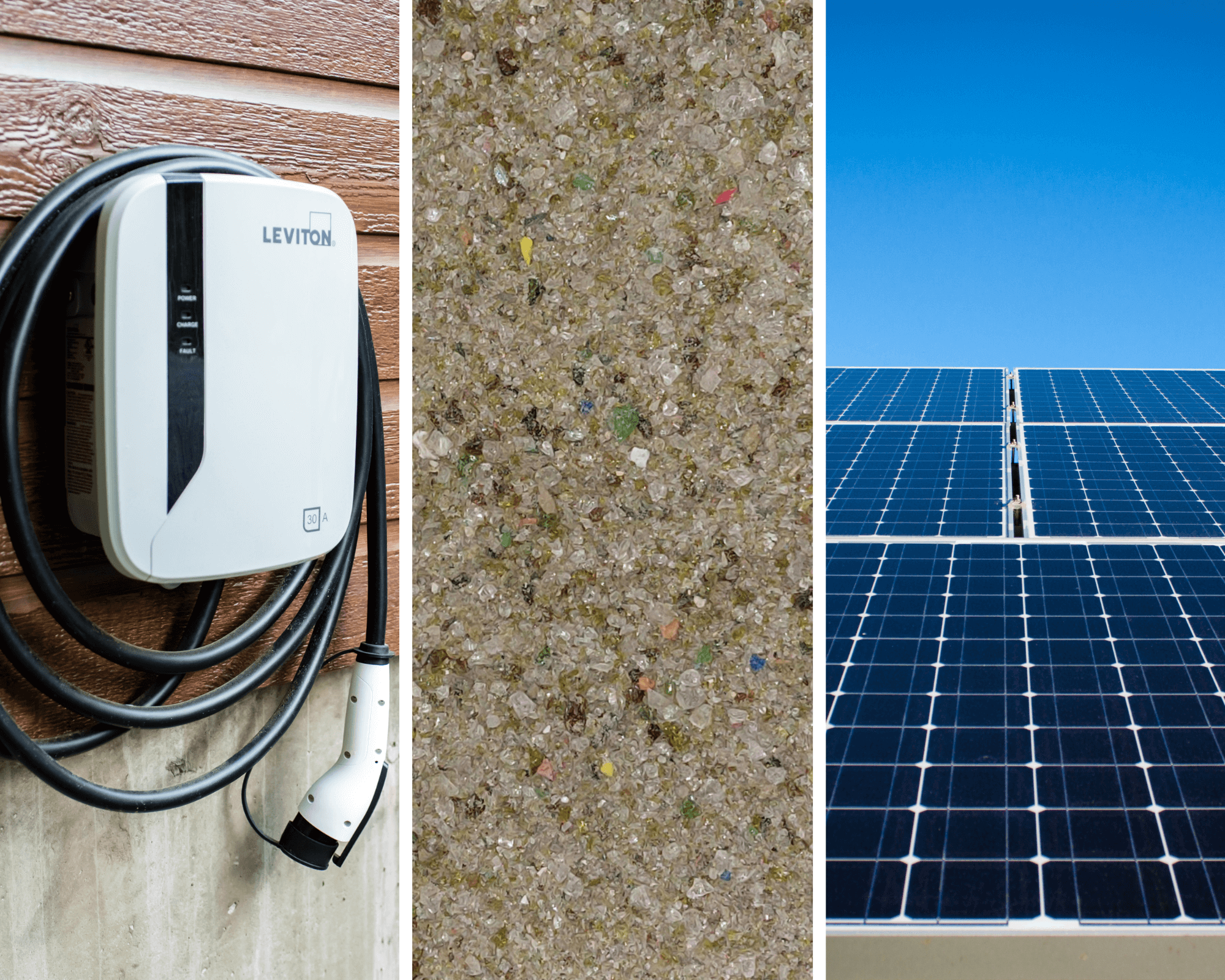
Research For Vermont: Evaluating EV incentives, creating new uses for recycled glass and helping towns install renewables
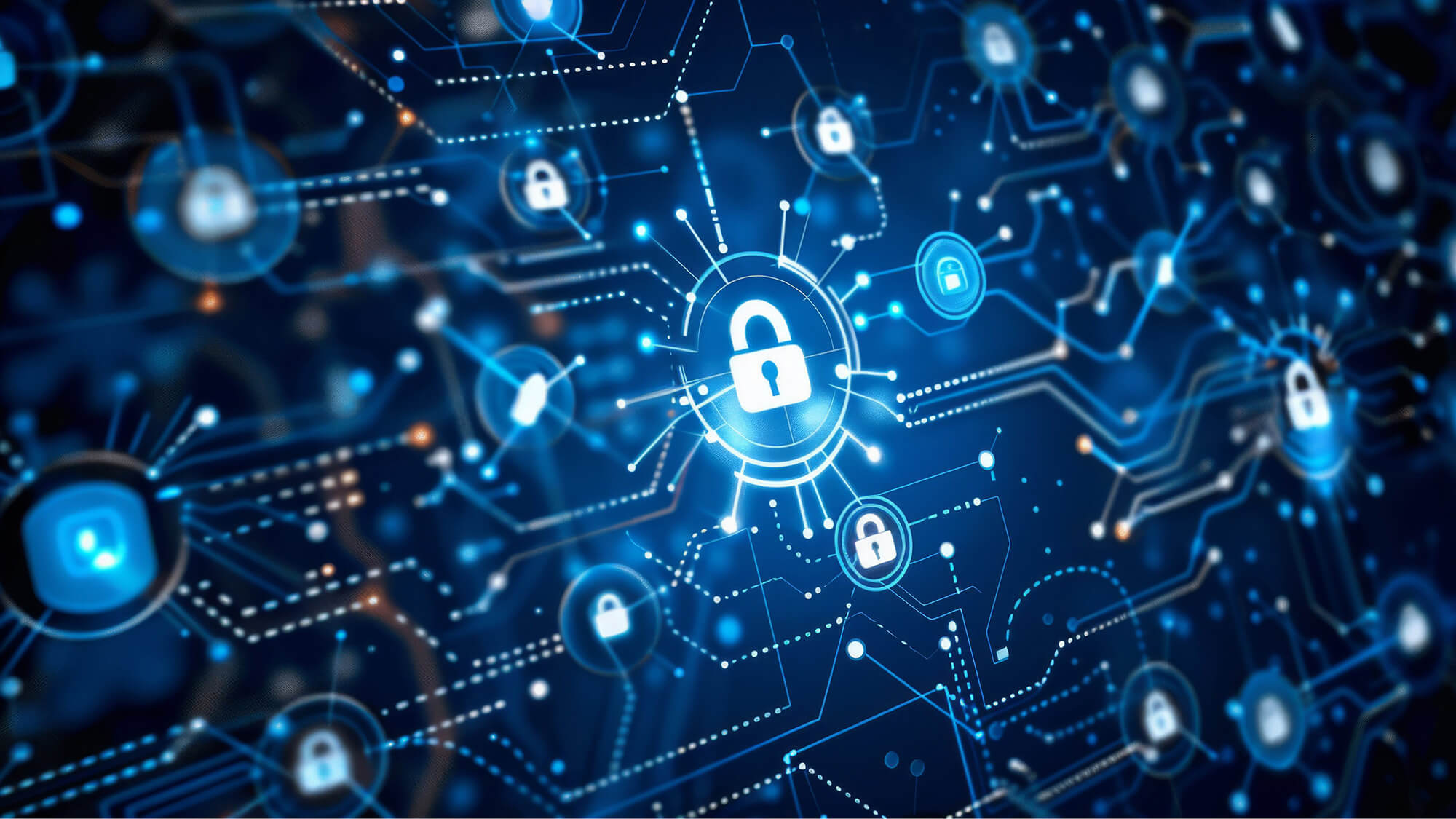
UVM Researchers Get Weird: Bringing Mathematical Rigor to the Science of Hidden Networks
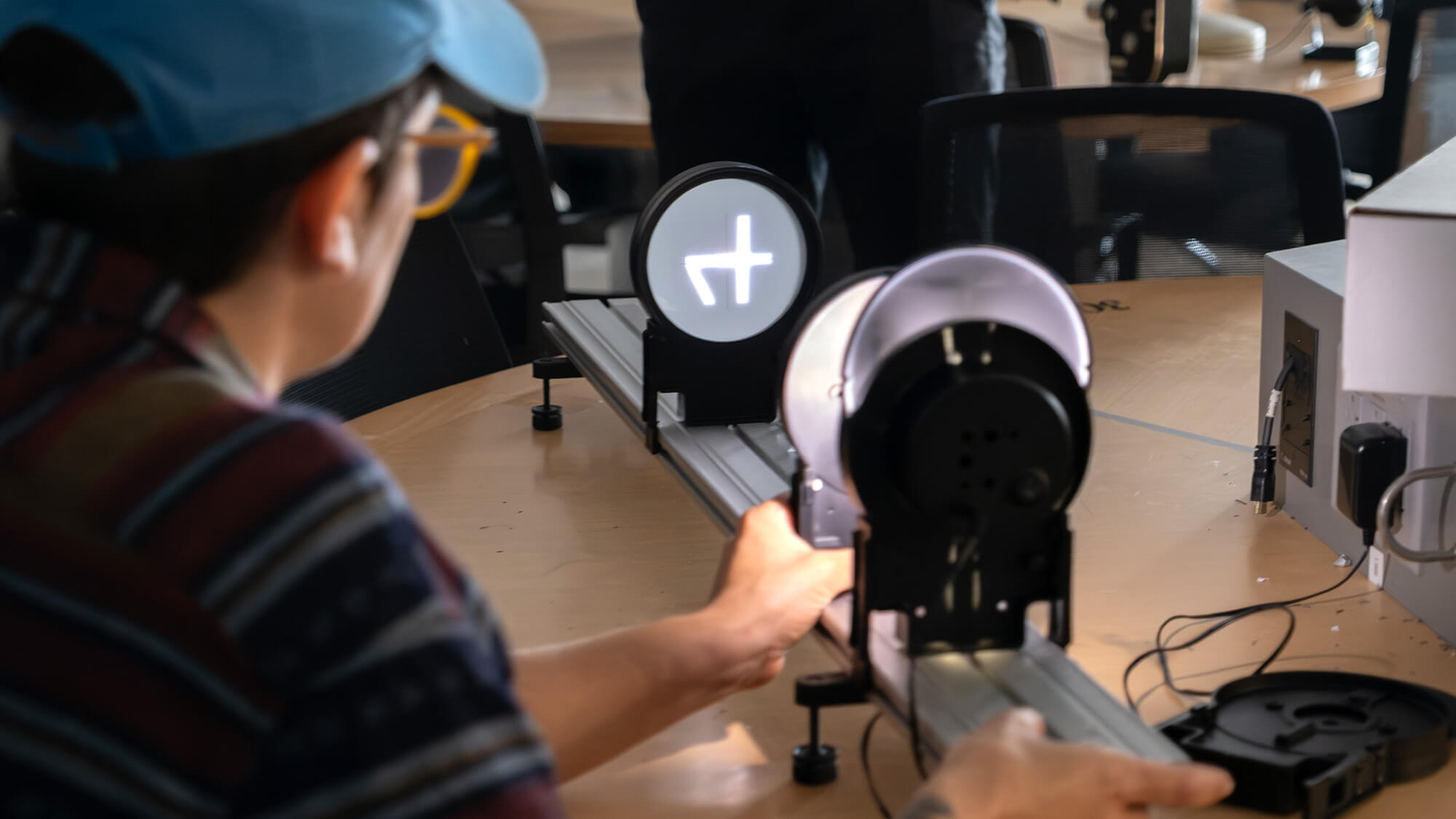
From Farms to Photons
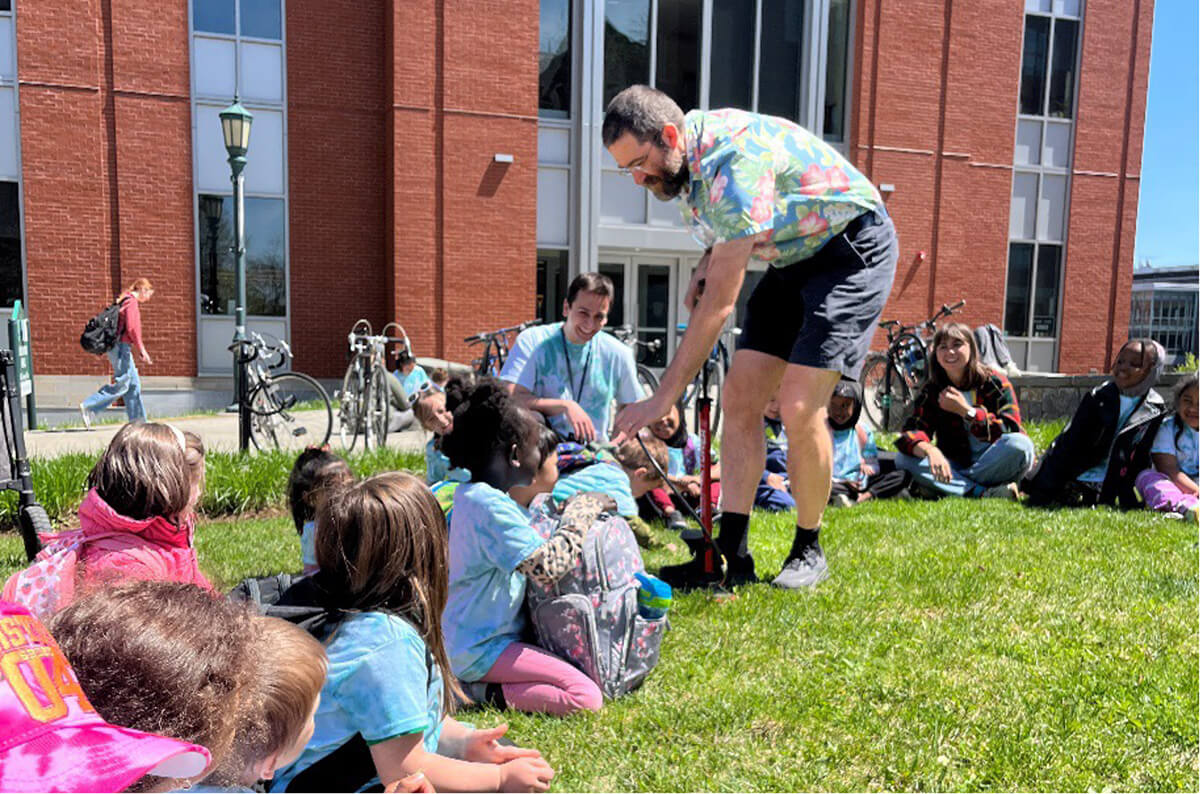
Local Kindergarten Students Treated to Tours and Physics Demos
Quick Links by Audience
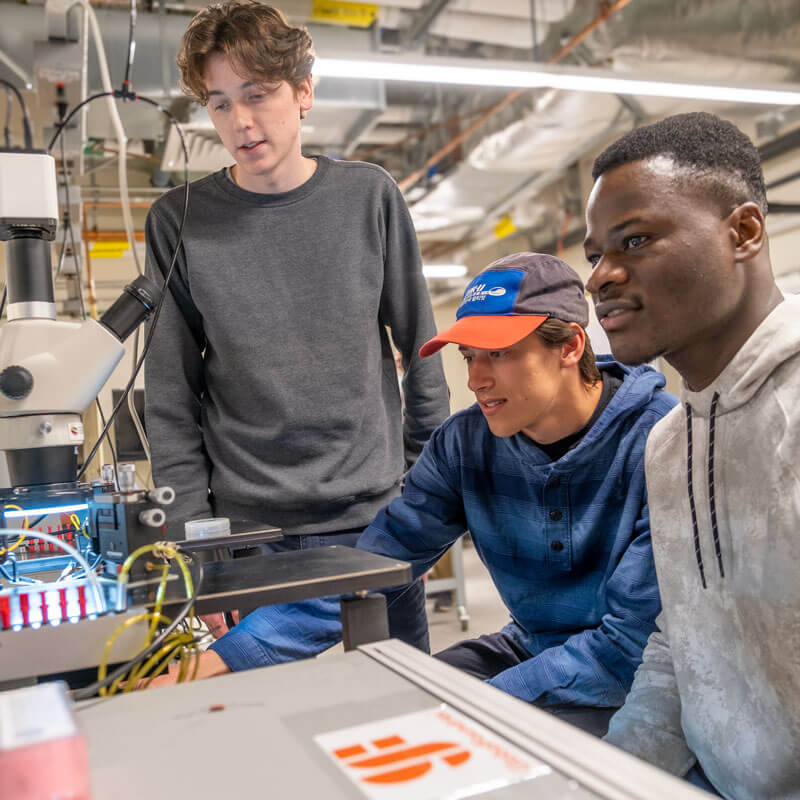
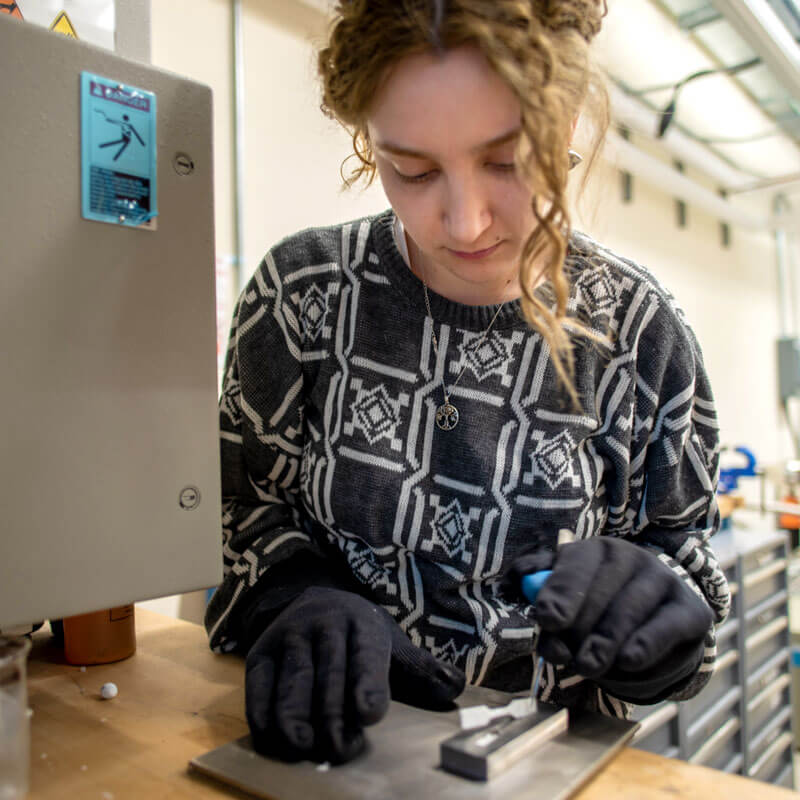
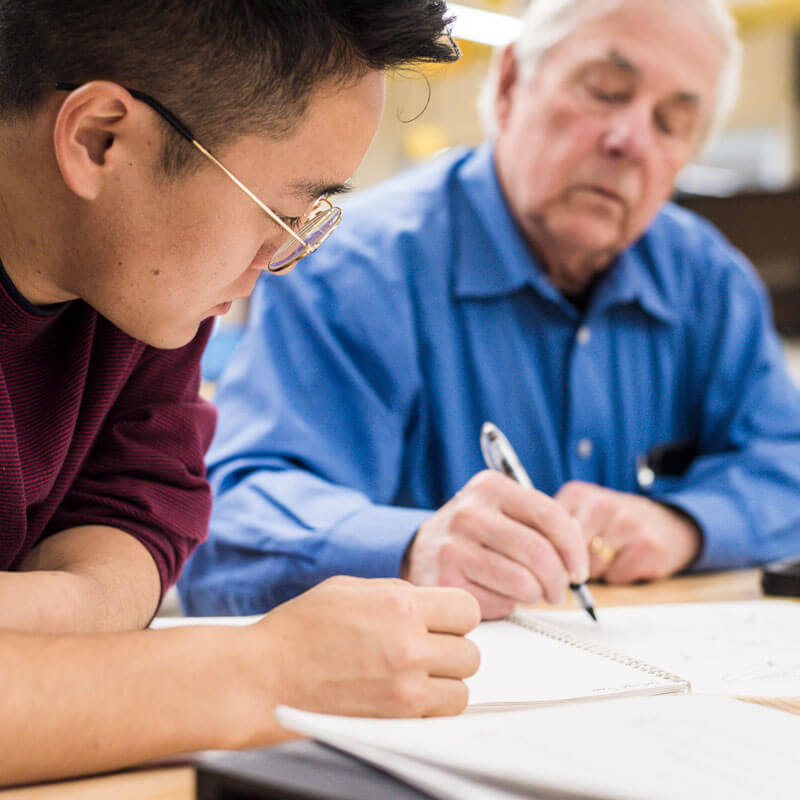