GetBlok Farms is an urban container farm in Aliquippa, just outside the city of Pittsburgh, Pennsylvania, that has a mission to provide freshly grown, local food to communities in need. They have a drive for innovation, fresh food and local economic development. Vinnie, the owner, shared with us how this business started as a technology company and provided employment, mentoring, and career opportunities for the area.
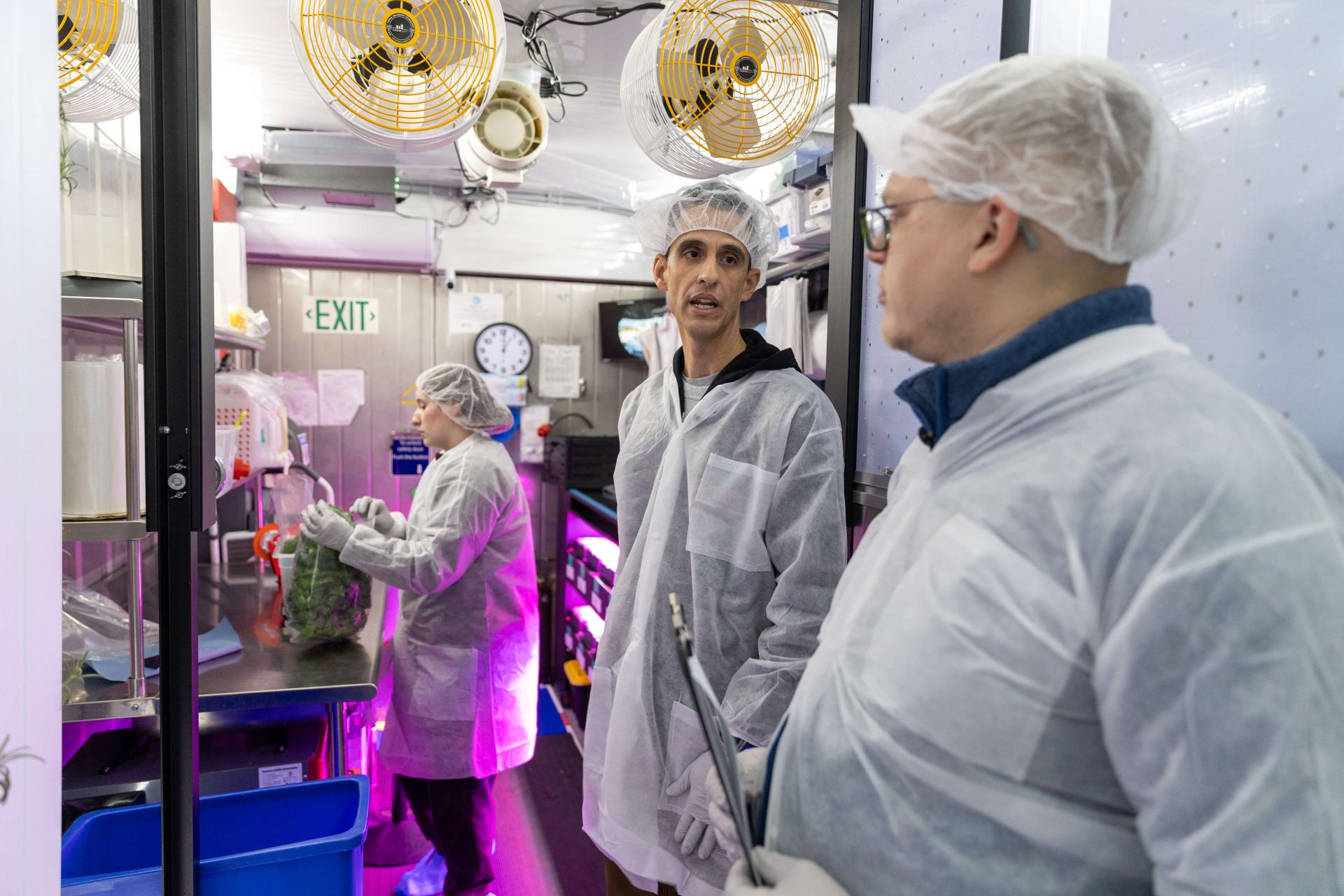
Sean Fogarty with UVM Extension and the Northeast Center to Advance Food Safety visited to learn what produce safety looks like in a hydroponic container farm, and observed a very high level of attention to detail at this farm. Upon entering the container it is common practice to wash hands, don gloves, booties, and hair nets. The decision to implement and uphold these practices comes from a goal to have a high level of quality, and is a result of their IPM (integrated pest management) strategy to minimize pests from entering this highly controlled facility.
Background
Inside the containers they grow a variety of crops including red leaf lettuce, romaine, arugula, hakurei turnips, Parisian carrots, and herbs. These crops are grown year round, and ideally in a “just-in-time” manner which is scheduled based on seasonal demand. There can be 3-4 people working in one container at a time, to harvest from a panel, harvest on the table, package, or seed.
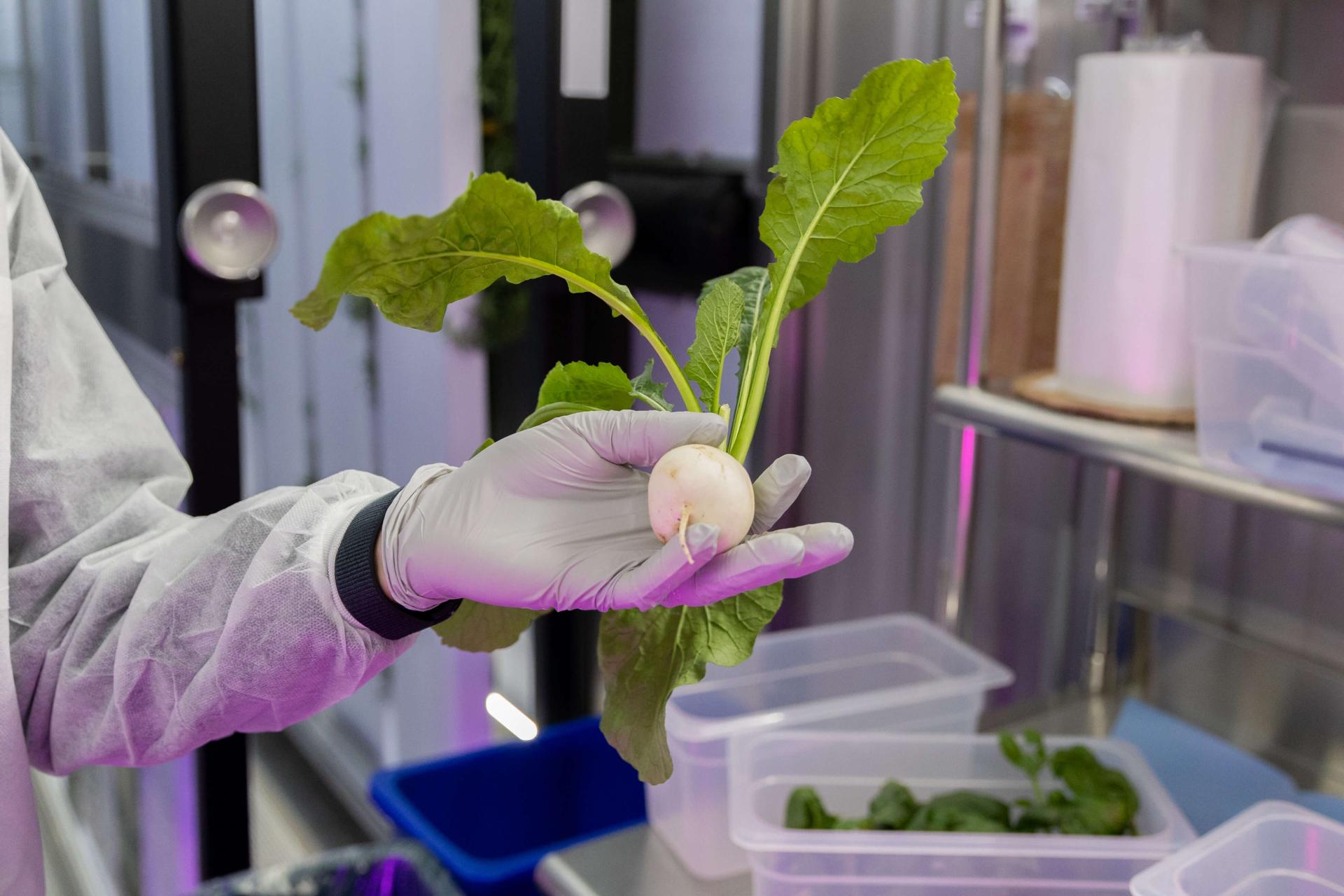
Watch the Interview with Vinnie
Details of Container Farms
The container is a standard, insulated shipping container of 8’x40’ size and is a kit offered by Freight Farms which has engineered and designed this container farm model for broad adoption by urban farming entrepreneurs.
Each container is set up the same way with a coat hook, sticky mat to step on, PPE (personal protective equipment) station and hand wash sink at the entrance.
Once you step inside there is a workspace on each side of the central walking path. One side houses the computer, seeding station, and environmental controller. Opposite of that is the packing station consisting of a stainless steel table and shelf where products are harvested and bagged before exiting, minimizing the risk of outside contamination.
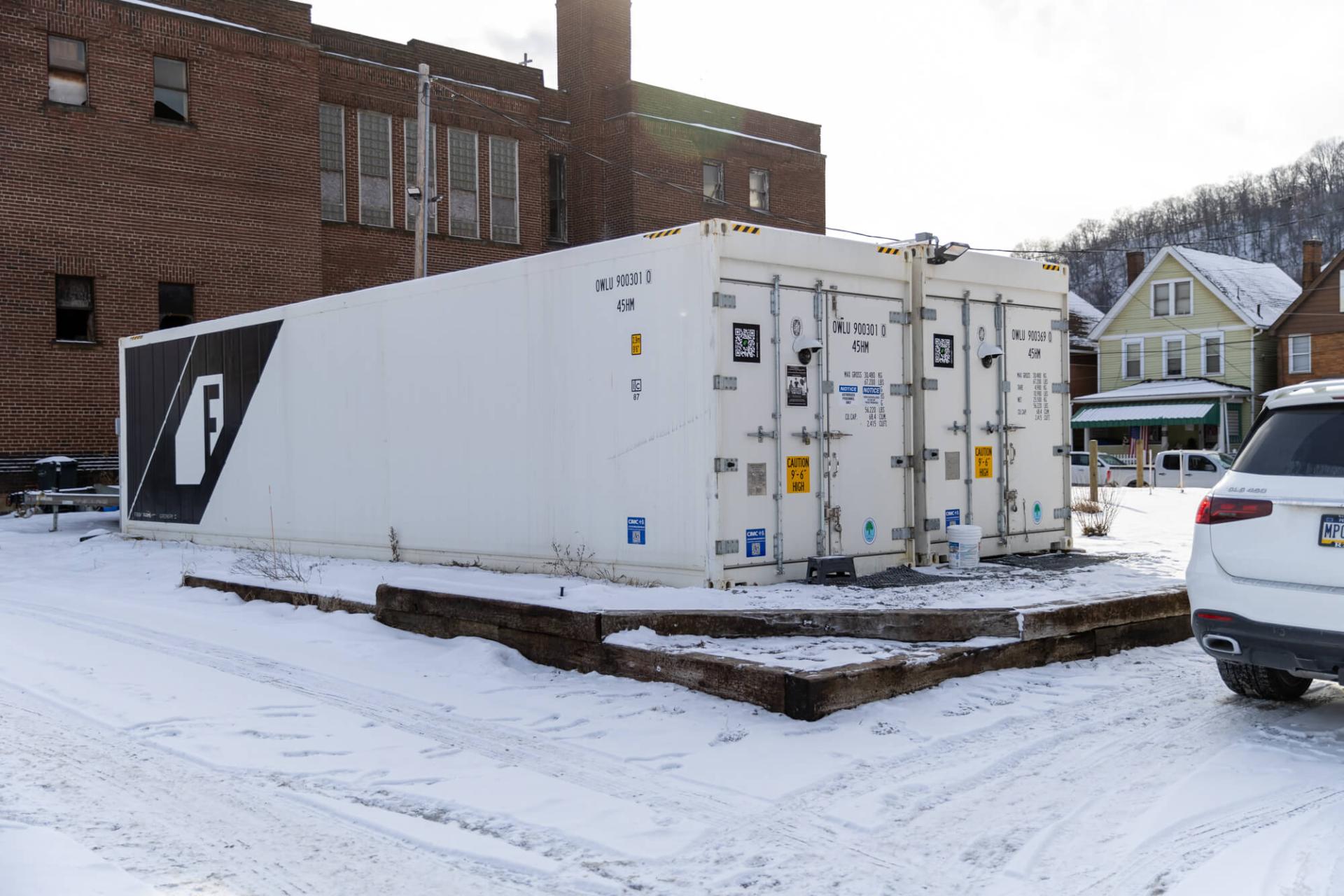
Seeds are started in plugs of a peat moss-derived substrate in the nursery area before getting transplanted into the cultivation area. Crop planning happens on a weekly schedule.
The farm is controlled via automation software, which monitors the water PH and electrical conductivity and controls the dosage of nutrient solution, light intensity, and blue/red light ratio based on the needs of specific crops and growth stages.
Though the hardware was provided in this turnkey system, it was up to the GetBlok team to create their own intellectual property and procedures to make the farm work economically, with consistency and efficiency.
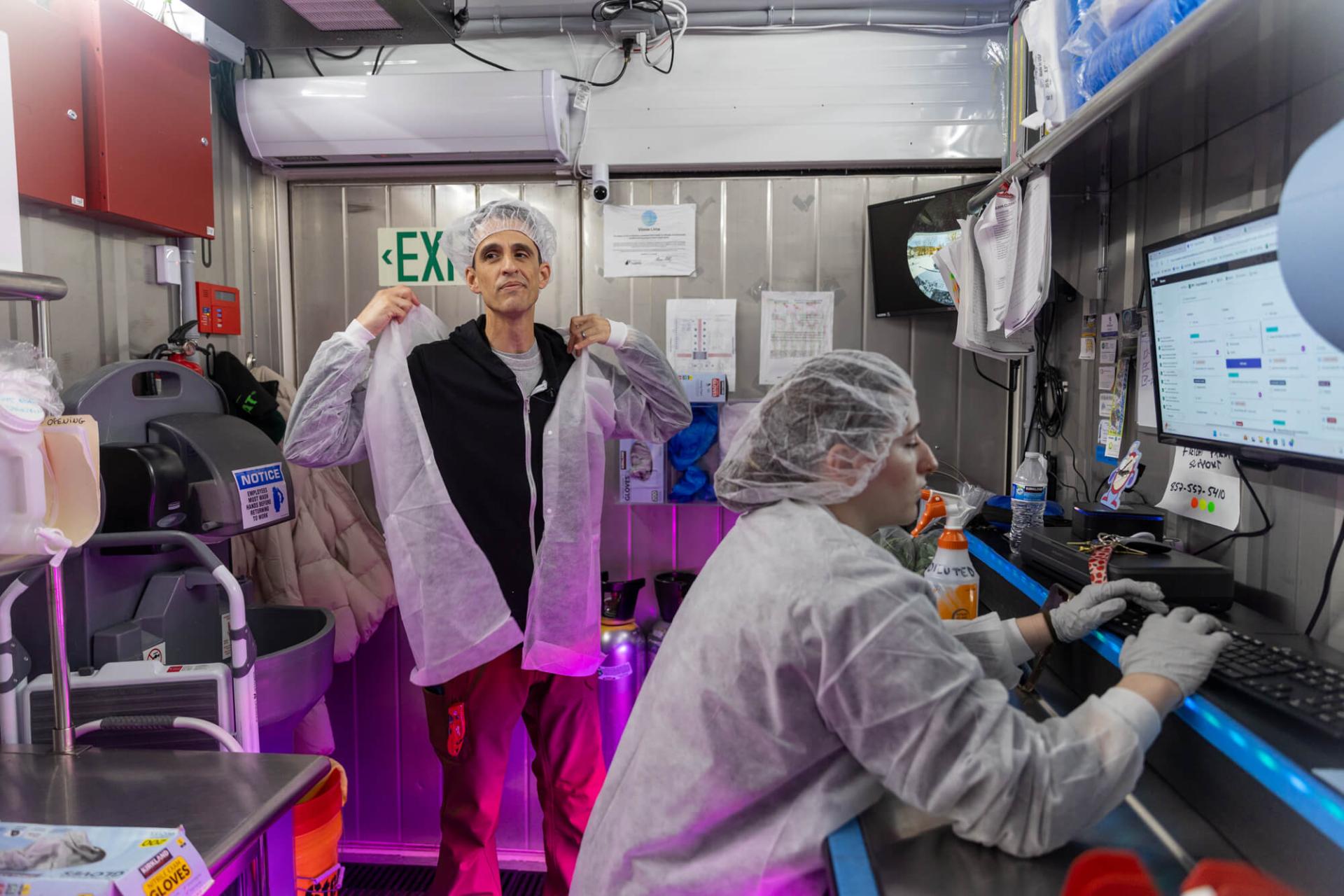
Three Components of IPM Controls
- Biological controls: Use of beneficial bacteria in irrigation water
- Mechanical controls: PPE use, air purification, surface sanitization, fly traps (these help to keep fungus gnats at bay, for example)
- Scouting crops frequently for any indication of spores, mold, pests, etc.
Approach to Food Safety
Food safety is a layered approach made up of various elements. The following are all contributors to a culture of food safety.
- Everything is hand trimmed (harvested) so it gets a visual inspection before packaging.
- Food contact surfaces are minimal, including scissors, the harvest table, harvest containers, and the final packaging
- No produce gets washed, so this keeps the pack process simple and avoids adding risk associated with postharvest water
- Produce is directly handled only once, when it is harvested and packed
- Use consistent, certified suppliers for nutrients and other inputs like substrate
- ServSafe food safety training is provided for all employees (offered by Penn State)
- Personal protective equipment (PPE) is provided for everyone entering the farm to prevent accidental contact with produce and surfaces
- ATP surface testing is used to verify the effectiveness of cleaning and sanitizing procedures
- Quarterly professional water testing for PH, EC, coliform bacteria, and heavy metals
- Have an eye towards continuing improvement
- Ensure everyone follows written SOPs and other policies
- No pets permitted
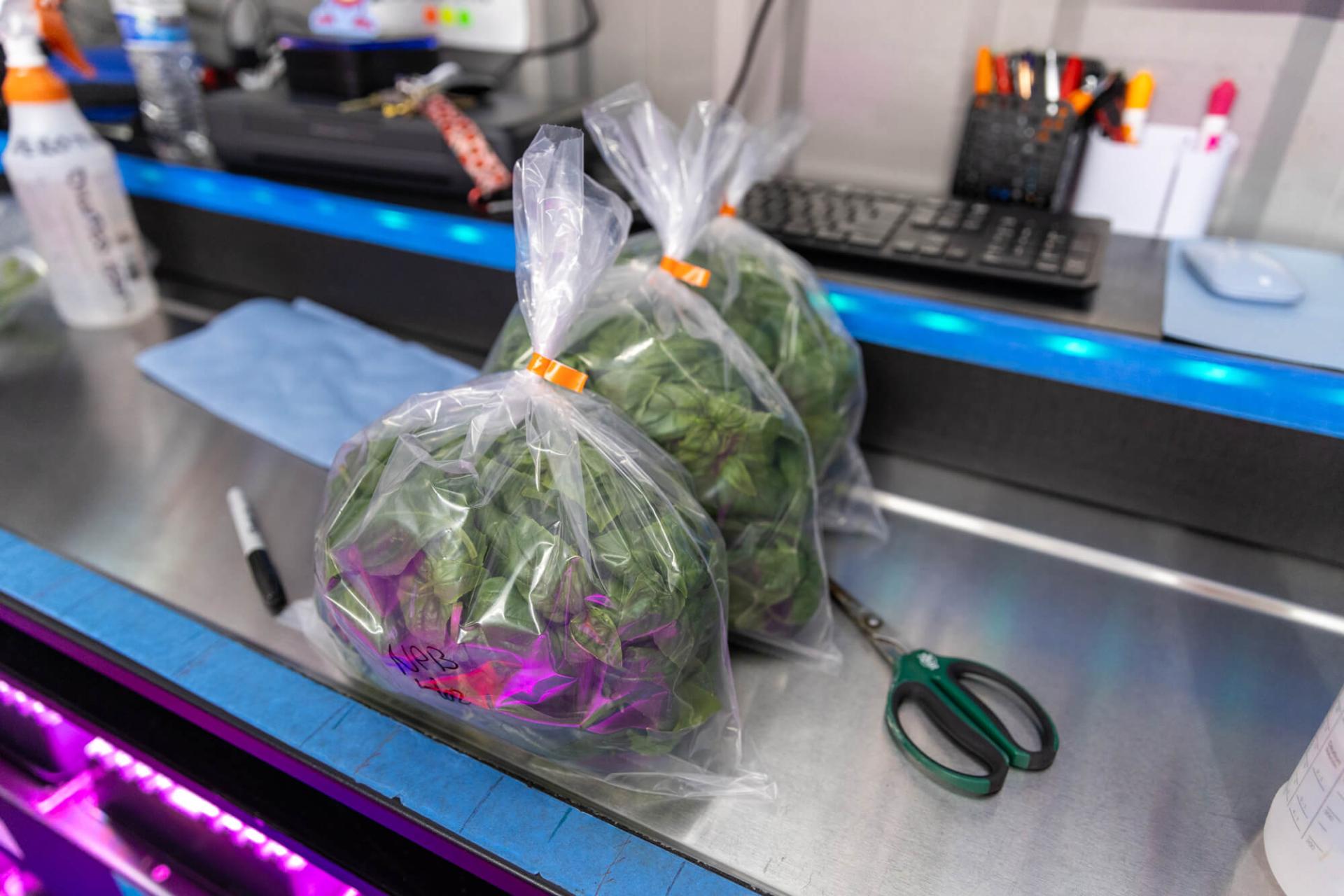
Sick Policy: Follow the ServSafe protocol. If you don’t feel good you cannot be in the farm. You may be able to work in headquarters, but not with the crop.
Hand Washing Policy: Wash hands any time you return to work, when replacing gloves, between crops, between tasks (harvest & cleaning). Use disinfectant on hands regularly.
Visitor Policy: Developed based on the USDA GAP (good agricultural practices) audit requirements. The farm is generally closed to the public for visitation, especially during harvest time. When visitors do come, they are asked to complete and sign an illness questionnaire before visiting. Staff observe visual cues for signs of illness before allowing visitor access.
Wildlife: Animals have not been a problem at this operation so far. Each farm is intensely well-protected from animal intrusion and outside environmental conditions to maintain the container growing environment.
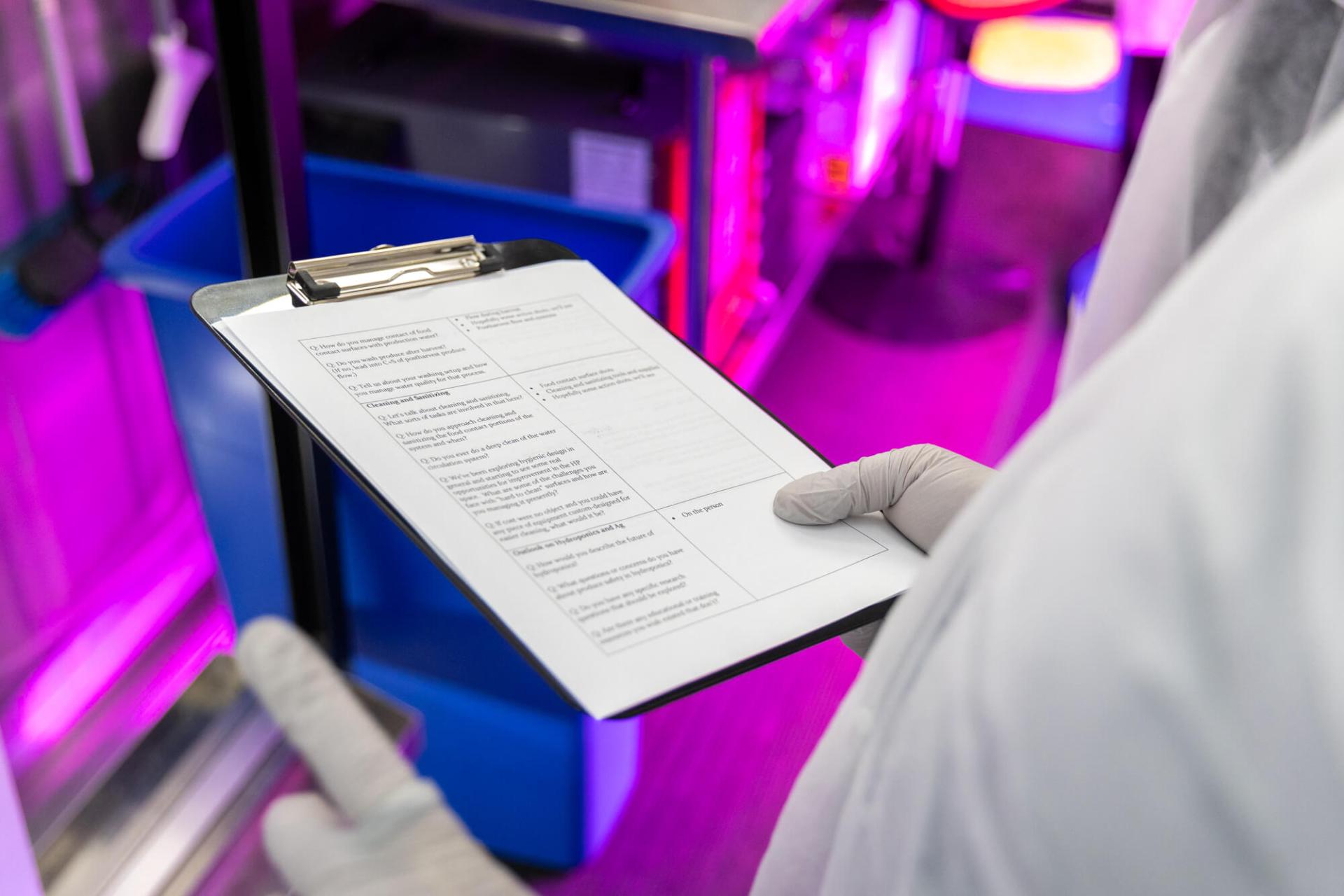
Water Management
There are various risks associated with indoor growing. What nutrient inputs you use and the quality of water used in production are two of the major factors. To reduce risk from the water, GetBlok uses municipal water, but only after it goes through a 3-stage reverse osmosis (RO) filter and ultraviolet (UV-C) treatment process. This provides a consistent baseline water quality, so nutrients can be dosed automatically with consistent results. Nutrients are sourced from trusted suppliers who certify their products’ quality.
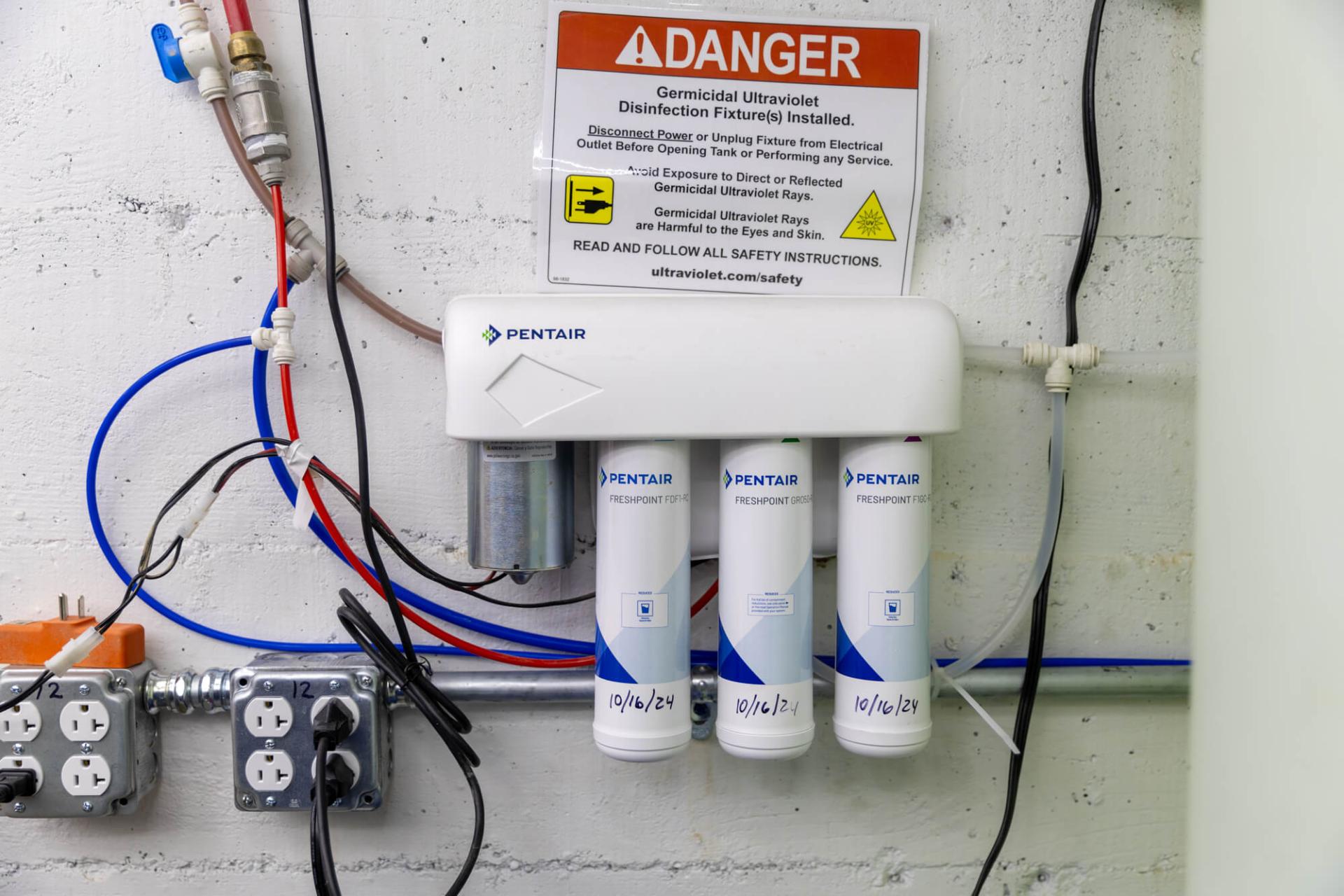
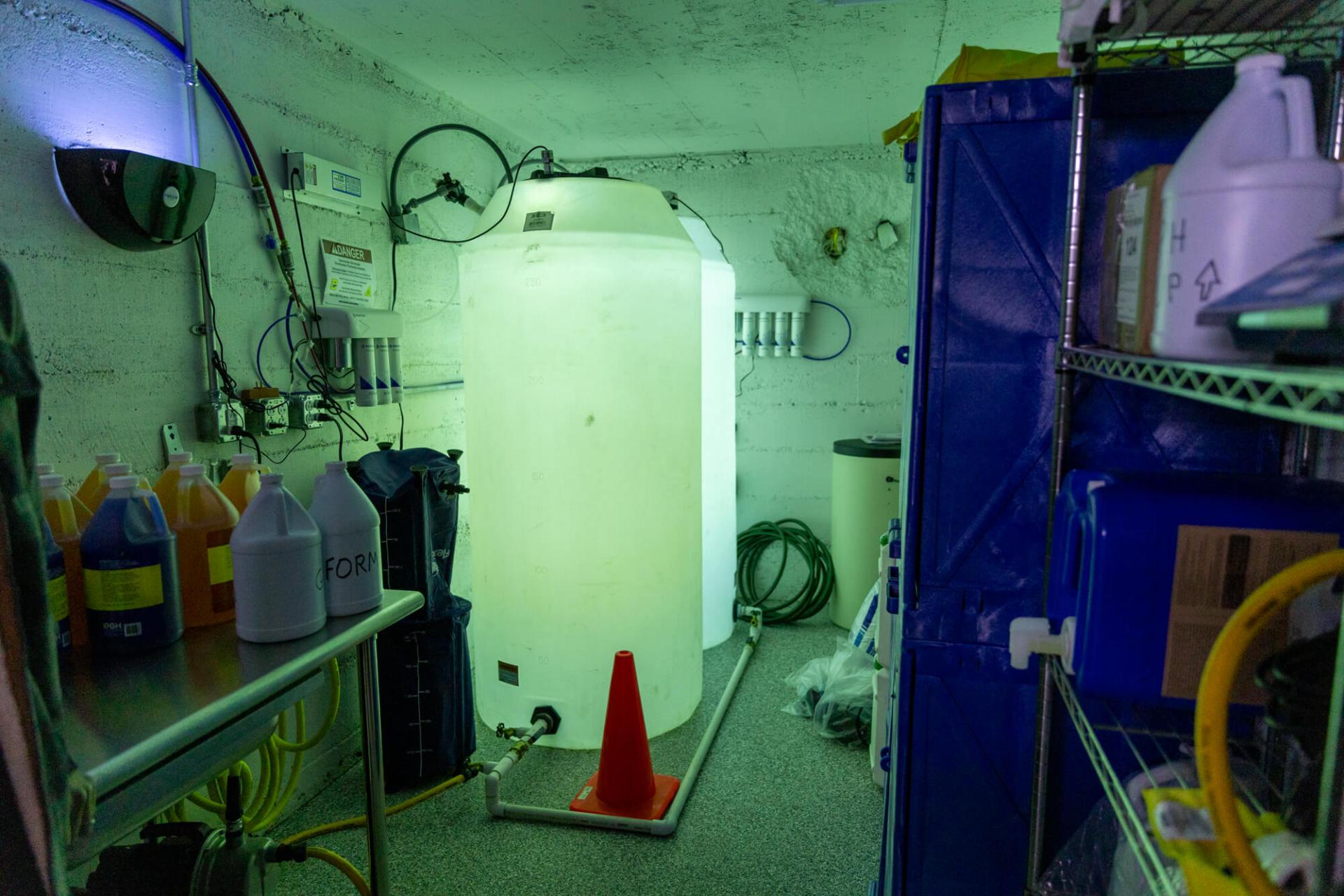
Common SOPs (Standard Operating Procedures)
GetBlok developed farm maintenance SOPs for tasks with varying frequencies, including daily, weekly, semi-monthly, monthly, quarterly and annually schedules.
These tasks include items like: replacing emitters, panel cleaning, cleaning and sanitizing growth media, replacing growth media, general farm cleaning, water turn-over, cleaning of water tanks, disinfection of circulation lines, wiping down shelves and counters, cleaning fans, etc.
Freight Farms provided some maintenance frequency guidelines as a starting point and GetBlok refined the schedule from there. They have also modified the off-the-shelf container farm with customizations to enhance the growing environment, for example by adding horizontal airflow fans (HAF) for increased air circulation to reduce, which helps to reduce tip-burn.
System Cleaning
Vertical growing panels are made up of three main parts: plastic channels, foam, and wicking strips. These components get cleaned after each use to minimize growth of microorganisms, including human pathogens, plant pathogens, and spoilage organisms.
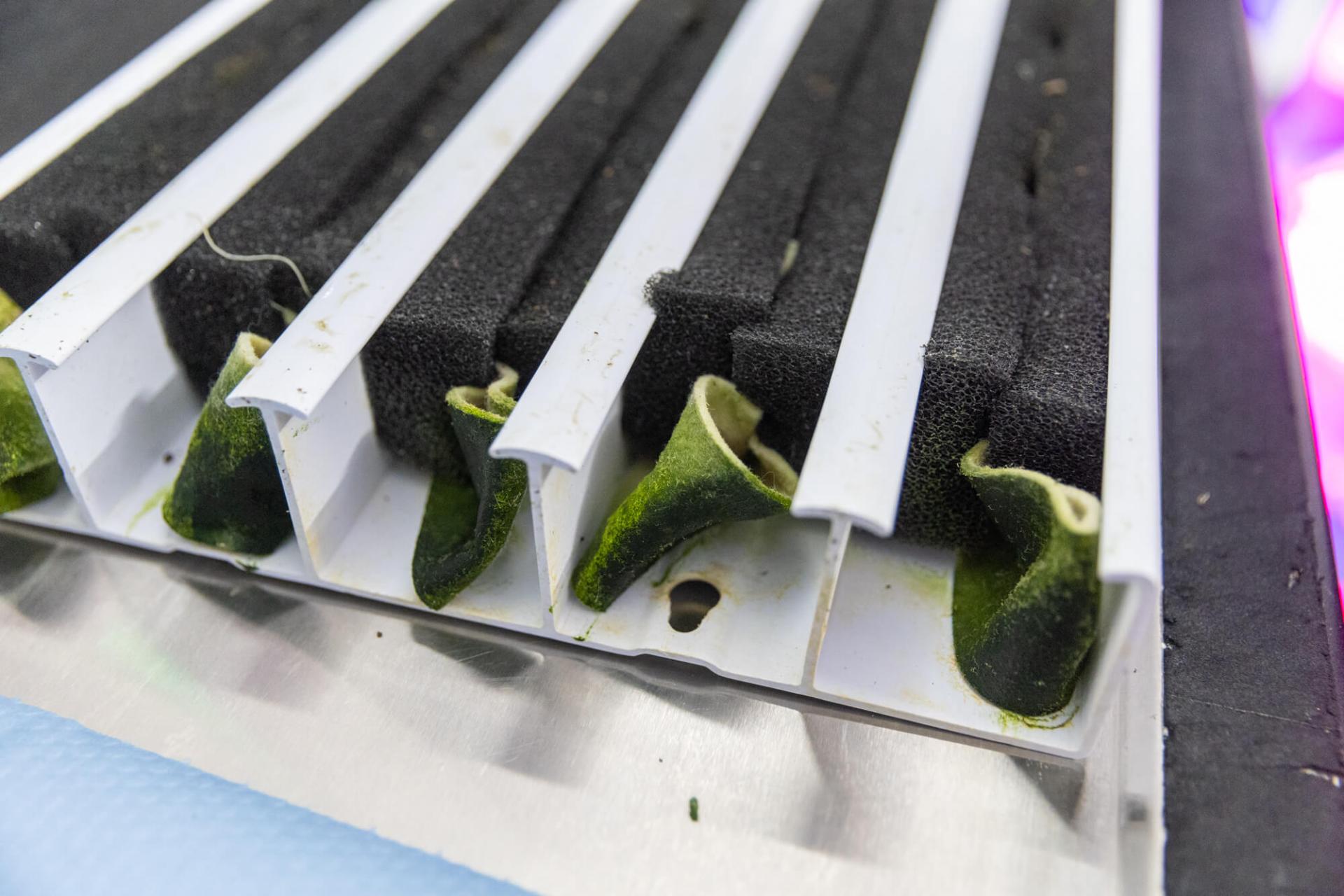
Cleaning procedure steps:
- Remove panels from the farm and transport to headquarters, where cleaning takes place
- Separate panel components
- Remove roots from foam (by hand)
- Wicking strips & foam:
- Wash (in washing machine)
- Sanitize (with peroxyacetic acid solution)
- Dry (in clothes dryer on high heat)
- Power wash & dry channels - This is done in a designated area with curtains to contain splashing and overspray.
- Shrink wrap the reassembled panels to keep them clean, then transport back to the farm
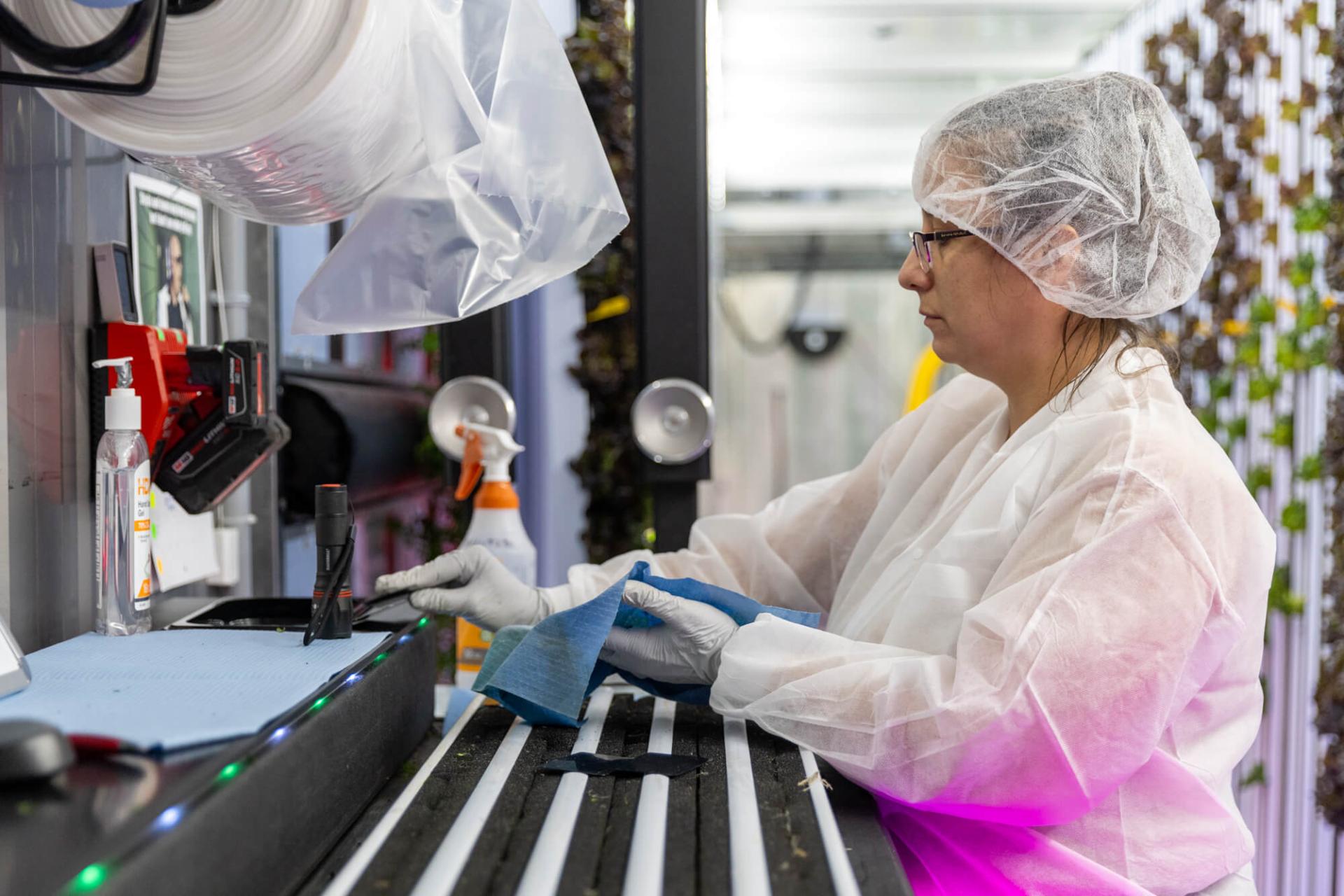
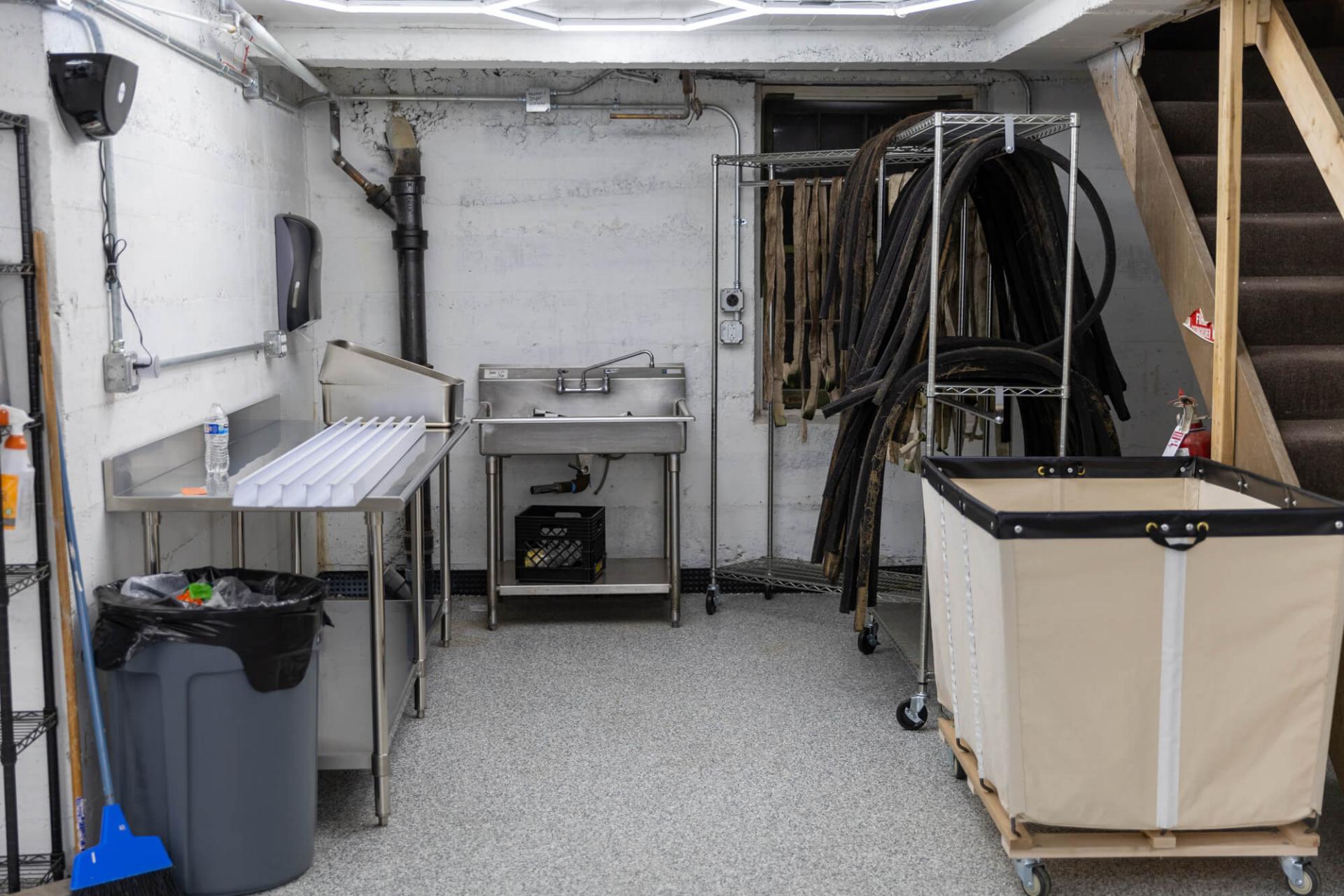
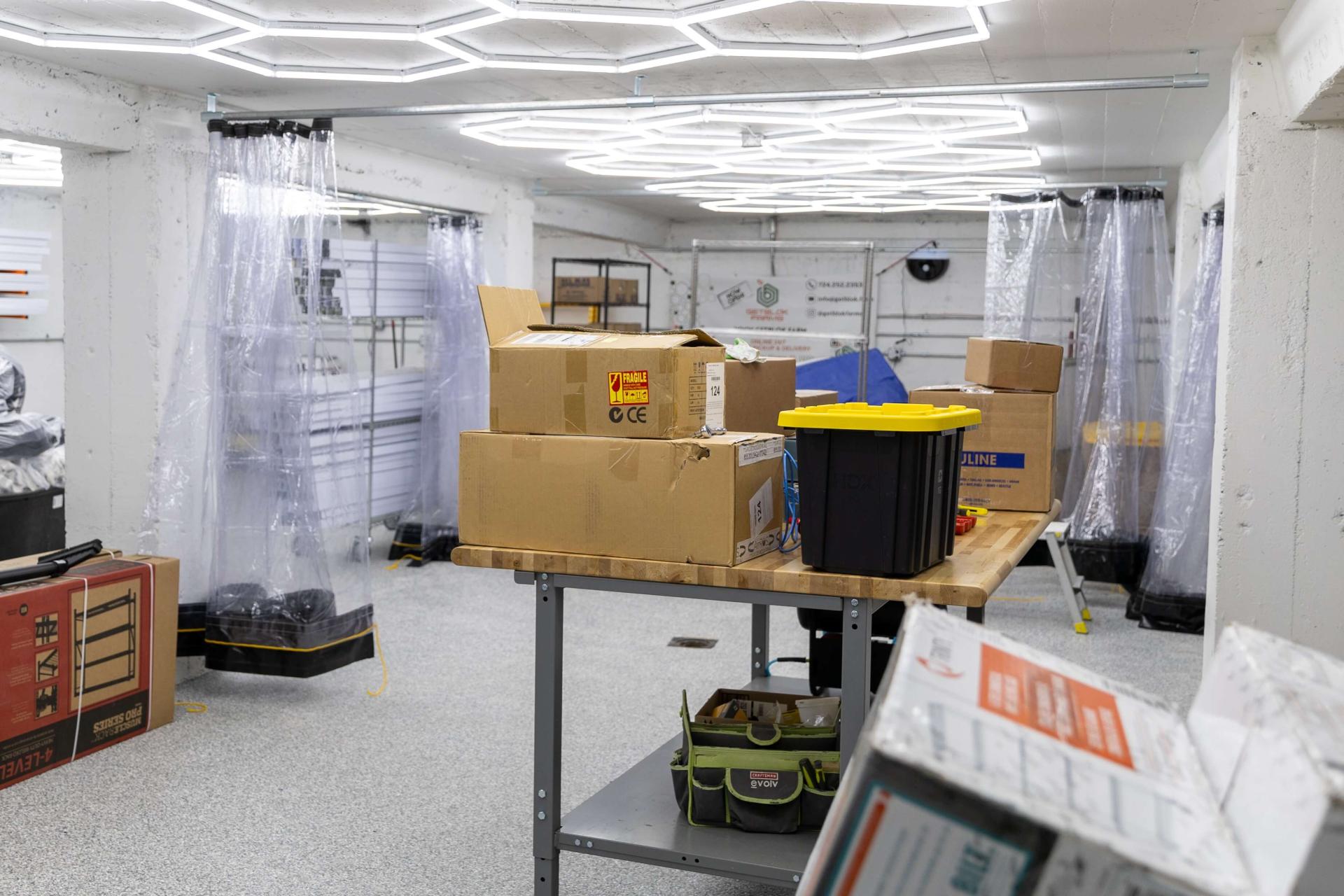
Share this post:
Acknowledgements
This work was supported by the Food Safety Outreach Program grant no. 2022-70020-01715 from the USDA National Institute of Food and Agriculture. Any opinions, findings, conclusions, or recommendations expressed in this publication are those of the author(s) and do not necessarily reflect the view of the U.S. Department of Agriculture.